5 QUESTIONS FOR is an interview series featuring cycling brands aiming to enhance their environmental impact reduction efforts. This series aims neither to showcase perfect examples nor to favour specific brands. What we do hope to offer is an informative and honest account of the possible challenges, gains and pitfalls of their journey. And to inspire more cycling companies to become part of this shared responsibility.
#012: Stijn Vriends, CEO of Vittoria

Vittoria S.p.A. is well-recognised in the cycling community for its tyre and accessories production and is also very committed to becoming more sustainable. Highlighting this commitment, they recently opened the world’s first CarbonNeutral® operations certified bicycle tyre factory. The facility in Bangkok features electric vulcanisation processes, solar panels on the rooftop, reliance on renewable energy, paperless operations and electric automated guided vehicles. These practices have earned the new factory the CarbonNeutral operations certification. At the recent Taipei Cycle Show, they also presented the Terreno PRO T60 Mixed, a new tyre made from 92% renewable and recycled materials.
In the following interview, we spoke with CEO Stijn Vriends about the company’s ambitions when it comes to sustainability, as well as the challenges, gains, and pitfalls during the journey towards more sustainability.
Mr Vriends, let’s begin with a look back. When did the topic of sustainability become more important to you?
Stijn Vriends: Sustainability has been in my focus for several years. However, I would say that we really started four years ago. At that time, we did a lot of research about the rubber industry and its environmental impact. It’s not a secret that this industry is not the cleanest one worldwide, so we wanted to understand how much CO₂ we accumulate as a company and as an industry. With the help of an online tool, we started to calculate our footprint, and the result was that, on average, the production of one bicycle tyre generates around five kilograms of CO₂eq gases – basically a whole meeting room filled with emissions. Since we produce 30,000 tyres per day, that means that we fill 30,000 meeting rooms every day with CO₂. And we are only one producer of many – I wanted to change that.

Vittoria is one of the biggest tyre producers in the bicycle industry, and you have more than 1,000 employees. Therefore, implementing changes might be more challenging than in smaller companies. How did you start the transformation process?
Stijn Vriends: The first step involved mapping out the current status and long-term goals. We had to get an overview of every environmental aspect of our business. We then quickly discovered that we could do better on many levels, so we decided to start by focusing on specific things – for example, measuring our carbon footprint. The next step was creating a team that deals exclusively with sustainability issues within the company. We also gave some senior managers a clear responsibility, a budget and a deadline. Additionally, each department is responsible for several sustainability projects to ensure that sustainability is part of the culture and responsibility of everyone in the company.
One of the main things we are working on is carbon neutrality. We want to reduce greenhouse gas emissions across our value chain, starting from our operations. Our new factory in Thailand is CarbonNeutral® operations certified.
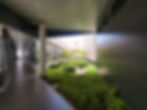
To achieve the certification, we have done the following things:
Invent a new process for vulcanising the tyres, switching from gas and steam to electricity.
This change reduces energy intensity by more than 50%.
Switch to renewable energy sources for our electricity use. In our new factory, we have solar panels installed. The remaining energy is sourced from certified suppliers that guarantee renewable generation.
Support carbon offsetting projects that plant trees and protect nature worldwide through Climate Impact Partners.
Another thing we are working on is circularity. We want to make our products using fewer new materials and more renewable or recycled materials. They should also last longer and be more recyclable. To achieve this, we have done things like:
Use natural rubber and bio-based materials in our tyre compounds.
Use renewable materials like cotton and recycled nylon in our tyre casings.
Take back and recycle our old products.
What has been your most difficult challenge so far?
Stijn Vriends: I think the most difficult challenge, in general, is to focus on the right things at the right time. Sustainability is a big and complicated topic, and trying to do everything at once can be overwhelming. You would rather avoid getting lost in 200 different goals and set impossible targets that are too far in the future. Therefore, we needed to focus on specific factors to create the most significant change as soon as possible. One example is material research. With so many different products, finding materials that can replace our current portfolio will take us many years. But we see the light at the end of the tunnel. With the new Terreno PRO T60 Mixed, we have recently presented a tyre that is our first bicycle tyre almost entirely made of renewable and recycled materials.

Another thing we learned is that you need to be honest, accountable, and credible. It became clear that we have to be open and honest about how much CO2 is created in the bicycle tyre industry. We know now that for each tyre of circa 0.5 kg produced, on average, approximately 5 kg of CO2eq is generated by the overall industry. We do not hide that anymore. Furthermore, we want to prove our commitment and credibility by following the best practices and principles of sustainability reporting, such as the Global Reporting Initiative. We have published our sustainability reports since 2022. In the coming months, we will start publishing the carbon footprint of each of our products in our catalogues and on our website.
You say that you have started to report about your actions. What feedback do you get from your customers when it comes to sustainability?
Stijn Vriends: There is a lot of interest, and people talk about it. But it is too early for proper feedback. We also know that it will take more time and transformation steps before we can communicate our actions in a bigger way. In the future, we will be able to share the CO₂ impact of each of our products and put the information on the packaging and our website. Consumers then will be able to compare the environmental aspects of the products in a much more customer-friendly way.
However, one of the challenges is the lack of awareness and demand for sustainable products among consumers. Many cyclists don’t know or don’t care about the environmental and social impact of their cycling choices. Many cyclists also care more about price, performance, and looks than about sustainability when buying their products. We need to educate and inform consumers about the benefits and value of choosing sustainable products for themselves, the environment, and society.

Vittoria is just one of many players in the bicycle industry. What do you expect of the cycling industry on this journey towards more sustainability?
Stijn Vriends: I firmly believe that our industry can do better. Sustainability should be a common goal. Therefore, we have to put more effort into increasing the collaboration between companies. For example, there is still a lack of regulation and standardisation in the industry. There is no clear and consistent definition of what makes a product sustainable, nor a clear and consistent way of measuring and reporting the sustainability performance and impact of the products. There is also no certification or labelling scheme that can help the consumers identify and compare the sustainability features of the products. This creates confusion and mistrust among the consumers and the stakeholders and also slows down innovation and collaboration within the industry. We need to agree and adopt common and credible criteria and indicators for sustainability and verify and disclose them in a transparent and comparable way.
Another issue is that the bicycle industry is too fragmented. For example, while car tyres are being reused and recycled worldwide, there is no standard procedure for recycling bicycle tyres. But I’m convinced that all those things will happen at one point. That has to be the goal for the industry.
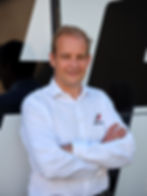
Mr Vriends, thank you for the interview.
Find out more about Vittoria here:
www.vittoria.com Photo credits: Vittoria, Werner Müller-Schell & Shift Cycling Culture